DIY Solar Panels: Complete Guide to Building Your Own Solar Power System
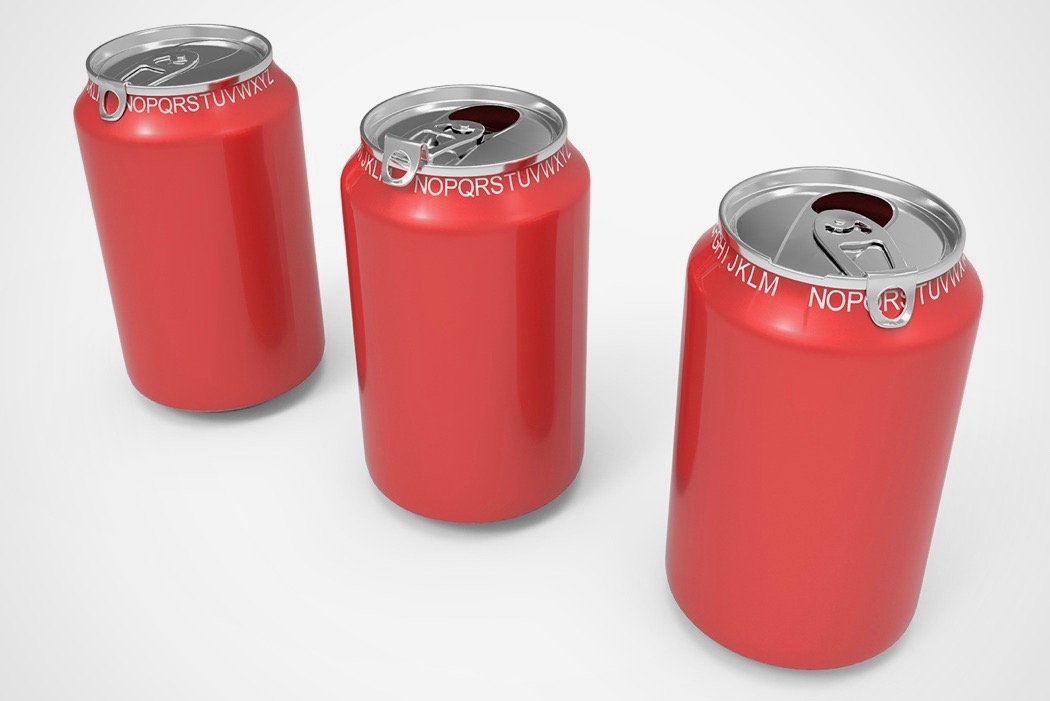
Understand DIY solar panel basics
Build your own solar panels represent one of the nearly rewarding renewable energy projects homeowners can tackle. While purchase commercial solar panels remain the virtually common approach, create custom solar solutions offer unique advantages include cost savings, technical knowledge, and complete system control.
Solar panels convert sunlight into electricity through photovoltaic cells. These cells generate direct current (dDC)electricity when expose to sunlight. An inverter so convert this dcDCower into alternate current ( ( ) )ectricity that power household appliances and feed into the electrical grid.

Source: envocabulary.com
DIY solar projects range from simple portable panels for camp to complete home solar installations. The complexity depend on your technical skills, available time, and energy requirements. Most DIY enthusiasts start with smaller projects before attempt whole house systems.
Essential components for DIY solar panels
Successful solar panel construction require specific materials and components. Photovoltaic cells form the heart of any solar panel. Monocrystalline cells offer the highest efficiency but cost more than polycrystalline alternatives. Thin film cells provide flexibility but generate less power per square foot.
Tab wire connect individual solar cells in series to increase voltage output. Bus wire carry current from cell strings to the junction box. Flux paste ensure clean electrical connections between cells and wire. Eva (ethylene vinyl acetate )film encapsulate cells between the front glass and back sheet.
Temper glass protect cells from weather while allow maximum light transmission. The back sheet provide electrical insulation and weather protection. Aluminum frames offer structural support and mount points. Junction boxes house electrical connections and bypass diodes that prevent power loss from shaded cells.
Tools require for solar panel assembly
Professional quality tools ensure safe and efficient solar panel construction. A soldering iron with temperature control allow precise cell connections without damage delicate photovoltaic materials. Lead free solder create reliable electrical joints that withstand thermal cycling.
Digital multimeters measure voltage, current, and resistance throughout the assembly process. Flux brushes apply soldering flux equally across cell connections. Wire strippers prepare tabbing and bus wires to proper lengths. Glass cutters score temper glass to exact panel dimensions.

Source: dreamstime.com
Laminating equipment bonds all panel layers unitedly under heat and pressure. Vacuum chambers remove air bubbles from Eva film during lamination. Frame cut tools shape aluminum extrusions to precise measurements. Drill bits create mount holes in frames and junction boxes.
Step by step solar cell assembly process
Solar panel construction begin with careful cell handling and preparation. Photovoltaic cells are exceedingly fragile and crack easy under stress. Work on a clean, pad surface with adequate lighting and ventilation for solder operations.
Apply flux paste to cell contact points use a small brush. Cut tab wire to appropriate lengths, typically extend slenderly beyond cell edges. Heat the soldering iron to the manufacturer’s recommend temperature, ordinarily between 350 400 degrees Fahrenheit.
Solder tab wire to the positive contacts on the front of each cell. Flip cells cautiously and solder the negative contacts on the back. Connect cells in series by solder the positive tab of one cell to the negative tab of the next cell. This process continue until reach the desire voltage output.
Test each cell string with a multimeter to verify proper connections and voltage output. Document any cells that produce importantly lower voltages, as these may require replacement or reposition within the panel layout.
Panel layout and design considerations
Effective panel design maximize power output while ensure long term reliability. Cell space affects both electrical performance and thermal management. Cells place overly close unitedly may experience overheating, while excessive spacing reduce overall panel efficiency.
Standard panel configurations include 36, 60, or 72 cells arrange in rectangular grids. Smaller panels work considerably for portable applications, while larger configurations suit permanent installations. Consider the final installation location when determine panel dimensions and orientation.
Bypass diodes prevent power loss when individual cells become shaded or damage. Install one bypass diode for every 18 20 cells in the panel. Position diodes within the junction box to protect them from weather exposure while maintain easy access for maintenance.
String voltage must match your inverter’s input requirements. Most grid tie inverters accept wide voltage ranges, but off grid charge controllers have stricter voltage specifications. Calculate total panel voltage by multiply individual cell voltage by the number of cells in series.
Encapsulation and weather protection
Proper encapsulation protect solar cells from moisture, temperature extremes, and physical damage. Eva film provide the primary encapsulation material in most DIY panels. This thermoplastic material becomes permanently bond to cells and glass during the lamination process.
Layer assembly follow a specific sequence: temper glass, Eva film, solar cell strings, Eva film, and back sheet. Remove all air bubbles and foreign particles between layers before lamination. Flush small contaminants can create hot spots that damage cells over time.
Lamination require precise temperature and pressure control. Professional laminators maintain temperatures around 150 degrees Celsius while apply vacuum pressure to eliminate air pockets. DIY alternatives include modify vacuum bags and heat sources, though results may vary compare to commercial equipment.
Edge sealing prevent moisture infiltration along panel perimeters. Silicone sealants design for solar applications provide excellent weather resistance and UV stability. Apply sealant ceaselessly around all panel edges, pay special attention to junction box penetrations.
Electrical connections and safety systems
Junction box installation require careful attention to electrical codes and safety requirements. Position box on the panel backrest to minimize shade while provide cable access. Use weatherproof connectors rate for outdoor solar applications.
Install mc4 connectors for easy panel interconnection and maintenance. These industry standard connectors lock firmly while allow quick disconnection when needed. Ensure proper polarity mark to prevent reverse connections during installation.
Ground systems protect against electrical faults and lightning strikes. Install ground lugs on aluminum frames and connect to the main electrical panel ground system. Use copper ground conductors size accord to local electrical codes.
Fusing protect individual panels and wiring from overcurrent conditions. Install DC rate fuses or circuit breakers between panels and charge controllers or inverters. Size protective devices accord to manufacturer specifications and local electrical codes.
Testing and quality assurance
Comprehensive testing ensure DIY panels meet performance expectations and safety requirements. Initial testing begin during cell assembly with voltage and current measurements under control lighting conditions. Document all measurements for future reference and warranty purposes.
Flash testing simulate standard test conditions use calibrate light sources. Professional flash testers cost thousands of dollars, but DIY alternatives use halogen lamps can provide useful performance data. Compare results to individual cell specifications to verify proper assembly.
Insulation resistance testing identify potential safety hazards from damaged encapsulation or poor construction techniques. Megohm meters apply high voltages between conductors and grind to detect insulation breakdown. Minimum resistance values depend on panel voltage and local electrical codes.
Thermal imaging reveal hot spots and uneven current distribution within complete panels. Infrared cameras show temperature variations that indicate defective cells or poor connections. Address any significant temperature differences before final installation.
Cost analysis and economic benefits
DIY solar panel costs vary importantly base on component quality and project scale. Individual photovoltaic cells cost between $0.50 $1.00 per watt depend on efficiency and quantity purchase. Additional materials include glass, frames, and electrical components add roughly $$030 $0.50 per watt.
Labor represent the largest cost component in commercial solar installations. DIY builders eliminate installation labor costs while gain valuable technical knowledge. Notwithstanding, factor in the time value of your labor when compare DIY versus commercial options.
Efficiency differences between DIY and commercial panels affect long term economic returns. Professional manufacturers achieve higher cell packing densities and superior quality control. DIY panels may produce 10 20 % less power per square foot than equivalent commercial products.
Warranty considerations importantly impact total cost of ownership. Commercial panels typically include 20 25 year power output warranties and 10 12 year product warranties. DIY panels rely on component warranties and builder expertise for long term reliability.
Installation and grid connection requirements
Solar panel installation involve structural, electrical, and regulatory considerations beyond panel construction. Roof mount systems must support panel weight plus wind and snow loads. Ground mount systems offer easier access but require additional foundation work.
Electrical permits ensure installations meet local safety codes and utility interconnection requirements. Most jurisdictions require licensed electrician involvement for grid connect systems. Off grid installations may have fewer regulatory requirements but yet need proper safety systems.
Net metering programs allow grid connect solar systems to sell excess power stake to utilities. Notwithstanding, many utilities require certify equipment and professional installation for net metering participation. DIY panels may not qualify for these programs in some areas.
System monitoring help optimize performance and identify maintenance needs. Basic monitoring measures total power production, while advanced systems track individual panel performance. Wireless monitoring systems provide remote access to performance data through smartphone apps or web interfaces.
Maintenance and troubleshooting
Regular maintenance maximize DIY solar panel lifespan and performance. Visual inspections identify crack cells, loose connections, and physical damage from weather or debris. Clean panels monthly in dusty environments or areas with heavy pollen.
Electrical testing verify proper system operation and identify develop problems before they cause failures. Annual voltage and current measurements help track performance degradation over time. Compare results to baseline measurements take during initial installation.
Common problems include cell crack from thermal stress, connection corrosion from moisture infiltration, and bypass diode failures. Most issues require panel dismantling for repair, emphasize the importance of quality construction techniques and materials.
Performance monitoring help distinguish between normal seasonal variations and actual system problems. Solar output vary with sun angle, weather conditions, and ambient temperature. Establish baseline performance data to identify significant deviations require investigation.
Advanced DIY solar techniques
Experienced DIY builders can explore advanced techniques to improve panel performance and reliability. Concentrated photovoltaic systems use lenses or mirrors to focus sunlight onto smaller, high efficiency cells. These systems require precise tracking mechanisms but achieve higher power densities.
Bifacial panels capture light from both front and rear surfaces, increase total power output by 10 30 % in suitable installations. DIY bifacial panels require transparent back sheets and elevate mount to allow rear illumination.
Flexible panels use thin film cells conform to curved surfaces and reduce weight compare to rigid glass panels. Yet, flexible panels typically offer lower efficiency and shorter lifespans than crystalline silicon alternatives.
Building integrate photovoltaics (bBIPM)replace conventional building materials with solar generate alternatives. DiDIYiBIPMrojects include solar roof tiles, transparent panels for windows, and solar cladding for walls. These applications require specialized materials and installation techniques.
Create your own solar panels offer significant learning opportunities and potential cost savings for dedicated DIY enthusiasts. Success require careful planning, quality materials, proper tools, and attention to safety requirements. While DIY panels may not match commercial efficiency or warranties, they provide valuable experience and energy independence for committed builders willing to invest the necessary time and effort.